Used in this project
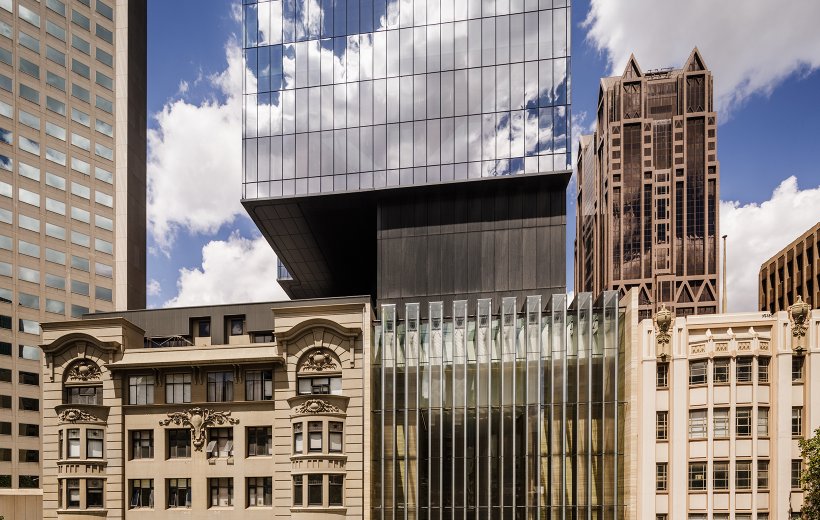
Steel delivers an additional 6,000 square metres of premium A-Grade lettable area.
405 Bourke Street is a 167-metre high, 40-storey tower, with a seven-level lobby space dubbed ‘The Lantern’. It provides more than 66,000 square metres of Property Council of Australia A-Grade accommodation and floorplates from 2,200 square metres.
The project
The series of glazed ribs that comprise the facade of the seven-level lobby space at 405 Bourke Street make a vibrant addition to the Melbourne CBD.
Dubbed ‘The Lantern’ and backlit at night for greater effect, it’s the street level element of a project that brings elegance and a robust sense of character to an industrious sector of the city.
An integral part of this tower is a 16-metre cantilever projecting over the heritage facade of 399 Bourke Street.
The main tower section above the cantilever features a beam and slab design approach using welded beams made from BlueScope XLERPLATE® steel.
Maximising the building’s lettable floorspace
The cityscape of Melbourne has changed dramatically over the last 15 years, but fortunately the prevailing wisdom today is to retain heritage facades.
The old foundry at 399 Bourke Street is such a building, and its facade dates back over a century and has heritage protection in place.
Developer Brookfield Properties owns 399 and co-owns 405 Bourke Street with Industry Superannuation Property Trust (ISPT), but the Heritage protection on the former caused a colossal challenge when it came to the redevelopment of the latter site, as the available space meant constrained floorplate sizes. And this would have a significant impact on the resulting building’s ability to attract premium tenants.
“The prevailing commercial logic with office buildings is to try and get a floorplate bigger than 2000 square metres and we achieved 2200 square metres,” says Woods Bagot principal architect, Simon Dick. “To do that we had to occupy as much of the site as we possibly could from Bourke Street all the way back to Little Collins.”
The only way to construct the $900 million, 167-metre high, 40-storey tower and include large floorplates to entice tenants was to cantilever over the 399 Bourke St’s protected facade. Woods Bagot’s architectural design vision utilised a cantilevered mega truss centered design that would support 32 office floors above to achieve this.
A structural engineer’s prefabricated steel solution for a lighter building
The original design for the building specified reinforced concrete mega-columns from the Ground Floor to Level 11, and the use of composite steel concrete-filled boxes for the cantilevered section. However, it was identified that due to the potential of axial shortening (compression of concrete mega-columns along their axis) and the potential of building movement, to deliver the architect’s original design intent the building had to be lighter to remain stable.
The building was to be kept as light as possible, while supporting 32 floors above the revised 16-metre cantilevered section. Following a structural engineer’s assessment of the design, constructing a lighter building could be achieved by replacing two of the original five concrete-filled fabricated steel mega-columns with prefabricated steel trusses, and introducing BlueScope’s prefabricated welded columns inside the remaining three mega-columns to strengthen them. The composite floor system using BlueScope welded beams and structural steel decking formwork made from BlueScope’s DECKFORM® steel, enabled the addition of a further three levels to the original design.
The project’s steel mega-column and truss centered design enabled a cantilever to be constructed over the adjoining Heritage building, which allowed larger floor sizes above.
The cantilevered mega-trusses: from concrete to prefabricated steel
The north-east portion of the tower cantilevers over the existing 399 Bourke Street via the use of three mega-trusses over a depth of three floors. Each mega-truss is approximately 28-metres long by 12-metres deep, consisting of 1.3-metre by 1.3-metre boxed steel sections.
The mega-trusses are constructed and held together with welds and bolted connections, with all the welds completed by hand. In total there were four kilometres of welds.
There was significant collaboration between the fabricator and engineer to deliver the best results.
The initial design for the mega-trusses included what steel fabricator Ron Kandell (Managing Director at GFC Industries) describes as “a box with reinforced concrete in them”.
“When we reviewed the initial design we had some major concerns with the potential for truss movement, so in collaboration with the structural engineers’ revisions, we proposed an alternative fully steel fabricated box solution,” explains Kandell. “We had to reduce the deflections of those big mega-trusses and the full-steel option gave us the best result.”
Eliminating concrete inside the mega-trusses reduced the size of the boxes by half and the weight by two-thirds.
“We took weight out of the structure, and the building movement became a lot more predictable,” he adds. “It was all put together onsite with bolted splices, it can be unbolted in the future, and the steel itself is recyclable down the track.”
Alternative design eliminates two mega-columns
The original design for the building specified five 40-metre concrete mega-columns from the basement to Level 11, however, two of the mega-columns were eliminated from the design with the introduction of specially fabricated welded columns inside the remaining three.
To reduce the concern of axial shortening in the mega-columns, maintain support for the steel cantilevered trusses, and reduce the building’s weight, the two front mega-columns facing the cantilevered trusses were strengthened with six metres of specially fabricated 800WC welded columns. These were placed within the mega-columns and then concrete encased.
BlueScope XLERPLATE® steel plate was used to strengthen the mega-columns and reduce the materials required and final structure weight.
Introducing the BlueScope 800WC welded columns into the concrete mega-columns allowed the loads from the 15-metre cantilevered mega-trusses to be successfully transferred to the two mega-columns.
In installing the cantilevered trusses and constructing the steel-based building, coordination between the Multiplex workforce and the architecture, engineering, and construction (AEC) professionals was paramount. “This meant very heavy elements needing dual tower crane lifts, acute design, planning, collaboration and supervision between Multiplex, structural engineer Robert Bird Group and steel fabricator GFC Industries,” says Cameron McMillan, project manager at Multiplex. “I believe the heaviest member was a Y node, which weighed around 32 tonnes.”
Weight saved
The removal of concrete from the cantilevered trusses and eliminating two entire mega-columns, according to Kandell, removed approximately 3,000 tonnes of steel and concrete from the original planned structure.
Primary tower
The main section of the building comprises a composite steel beam and slab floor system supported on full structural steel columns.
To maximise the office floor column grids, HISTAR® 460 HD columns with web and flanges up to 140 millimetres thick were adopted in the design combined with lighter BlueScope steel welded beams and columns.
“When you get to the typical office floor, the idea is to have it as column-free as possible, so the steel then makes sense again,” says Woods Bagot’s Dick. “You can do large spans with the beams because of its high strength to mass ratio. It effectively only requires columns in the perimeter and a single row of columns down the middle. That was as good as you can get in making those spans out of steel. Had we gone with just concrete, the spans’ overall thickness would have made the depth of the structure deeper, so there would have been fewer floors and therefore the building economics come into it.”
The optimisation of the steel structural system has allowed the floor height to be as minimal as possible, “which is always the game with high-rise commercial buildings,” adds Dick.
“Much of the steel used was from level eight of the build, above the existing structure, all the way up to level 40. They were huge 700WB steel beams, 0.7 metres in depth,” says Jack Withers, senior associate and structural engineer on 405 Bourke Street, Robert Bird Group (RBG).
From RBG’s perspective, this element required extensive coordination with the mechanical engineer to develop a strategy that minimised beam penetrations and beam notches.
The benefits of using such long beams included strength and speed of construction. “Because it’s steel, you get a lot of inherent strength,” says Withers. “You’re not constrained by a lot of the issues you have with concrete, where you have to wait for it to cure, back prop and do a number of things for temporary support. So, the average floor-to-floor cycle was something like four to five days, which is really, really good for floorplates of this size.”
GFC’s Kandell elaborates. “Composite floor design was adopted with BlueScope primary beams and precambered secondary beams with a structural formwork system. This system provided a typical grid system of 11.6m x 8.7m for a large portion of floor. I believe this system to be the most effective in relation to weight versus floor area. The use of BlueScope welded beams means longer spans, so you’re able to minimise the number of columns in the project.”
“Utilising bigger beams and larger spans reduces the number of crane lifts too.”
“Using an unpropped composite steel beam and slab design is a very efficient way of achieving the installation. The beauty of no back propping means that, once the floor is concreted, the very next day you can have other trades coming to put their services in.”
“With the decking system, BlueScope welded steel beams were fixed in place and the steel decking was installed. Sheer studs were then shot through it and into the beams for composite action with the concrete,” he adds.
RGB structural engineers also conducted options studies, testing a number of different possible decking systems for the building. Using the composite decking system, Jack Withers from RBG concluded that, “The foundations were lighter, the floors were easier to construct, and quality control was hugely improved.”
“This method meant quicker cycle times for the floors,” he explains. “You get far better quality control with a premade product from a factory that can be checked in a controlled environment, which is cut offsite and then brought to site.”
“There is a lot more confidence engineering wise… in terms of benefits, the material is minimised for the same output. Gaining three levels, or about 6,000 additional square metres of lettable area of premium real estate in the city using a steel composite beam and decking system as opposed to using concrete alone… in that sense, is a no-brainer,” said Withers.
Speed of construction and inherent strength were also key factors when choosing a structural formwork decking system as it further removes issues relating to using concrete exclusively, namely, waiting for it to cure and back propping, which can also be affected by bad weather. Onsite safety may also be improved as fewer workers and less time are required for the installation.
Use of BlueScope welded beams and structural formwork made from BlueScope DECKFORM® steel reduced the structure weight and permitted additional levels and a further 6,000 square metres of lettable floorspace within structural tolerance.
Sustainability
The steel elements are potentially reusable and recyclable as they have been connected by bolted splices and can be unbolted in the future. “It’s very difficult to reuse concrete,” says Withers. “You have to crunch it up, whereas steel beams you can disassemble and potentially reuse.”
Using prefabricated steel elements reduced the number of total crane lifts required for the build, generating less construction waste on-site as well as requiring fewer vehicle movements.
Project outcome
405 Bourke Street is an exemplar of urban regeneration done well – a significant project right in the very heart of Melbourne’s CBD. The design, fabrication, and construction teams faced many challenges, not just in solving the central issue of increasing the floorplate and lettable space by cantilevering over an adjoining building, but also other external obstacles. However, all these challenges were met and overcome resulting in a positive outcome for all stakeholders. And much of this was due to the primary material selected.
“The whole structure worked a lot better with steel. Frankly it was the reason that the project was a success in the end,” suggests Withers. “The steel that we used was great from an overall stability perspective, and from the finished look perspective as well. It was lighter and ultimately enabled us to get a lot more floors, which gave the client more building. Engineering-wise it was a great solution.”
“Working together as a united team utilising each other’s knowledge, experience, qualifications, commitment and everything else that goes with it, determined the outcome of this successful project,” concludes Kandell.
Award achieved
405 Bourke Street won the 2022 Victorian Institute of Architect’s Sir Osborn McCutcheon Award for Commercial Architecture, with the judges commending its creation of “a perfect floorplate within an imperfect site”.